Sculpture Design Customisation Service
Service process customer intention → project budget → contract intention → sign a contract → payment of deposit → factory order → design drawings → customer finalisation → production and installation → acceptance and settlement → after-sales service
Sculpture of each material production process
First, the production process of stone sculpture
Determined by the customer or provide sculpture reference pattern → clay craftsmen according to the customer's requirements plastic clay model → clay completed by the customer to confirm the confirmation of the clay draft turned moulds → turned gypsum model or glass fiber reinforced plastic model → stone sculpture craftsmen with stone sculpture production of special point modeling instrument for the production of stone sculpture → stone sculpture acceptance by the customer to confirm the acceptance of customer acceptance of the acceptance of the customer → shipments
Second, the production process of fibreglass sculpture
Determine or provide the sculpture reference pattern by the customer → clay sculpture craftsmen according to the customer's requirements to shape the clay model → clay sculpture is completed by the customer to confirm the confirmation of the clay drafts turn the mould (silicone mould) → production (imitation of stone, imitation of copper) glass fiber reinforced plastic sculpture products → glass fiber reinforced plastic sculpture to do the surface of the surface of the special surface treatment → sculpture production is completed → acceptance by the customer is complete → shipment
Third, the production process of bronze sculpture
Determined by the customer or provide the sculpture reference pattern → clay craftsmen according to customer requirements plastic clay model → clay completion by the customer to confirm the completion of clay → confirmation of the clay manuscript after the turnover of moulds (silicone moulds)
Small bronze sculpture production needs to use precision casting process → turning (paraffin) model → using quartz sand and other precision casting materials to make sculpture shell → baking shell dewaxing → firing shell → pouring copper water → to be cooled by the copper water and broken shell to complete the production of copper products → the surface of the copper products to do colouring, anticorrosion, as well as other treatments → the completion of the sculpture → the customer acceptance of the completion of the shipment
Large-scale bronze sculpture production needs to use resin sand casting → turn the glass fiber reinforced plastic model → according to the process requirements of the whole or piecewise casting → use resin to make the shell → after the resin shell casting copper water → after the cooling of the copper water, broken shell bronze sculpture casting is completed (such as piecewise casting needs to be welded and assembled to form) → the surface of the bronze products to do coloring, anticorrosion, and other treatments → the sculpture production is completed → the customer acceptance is completed → shipment
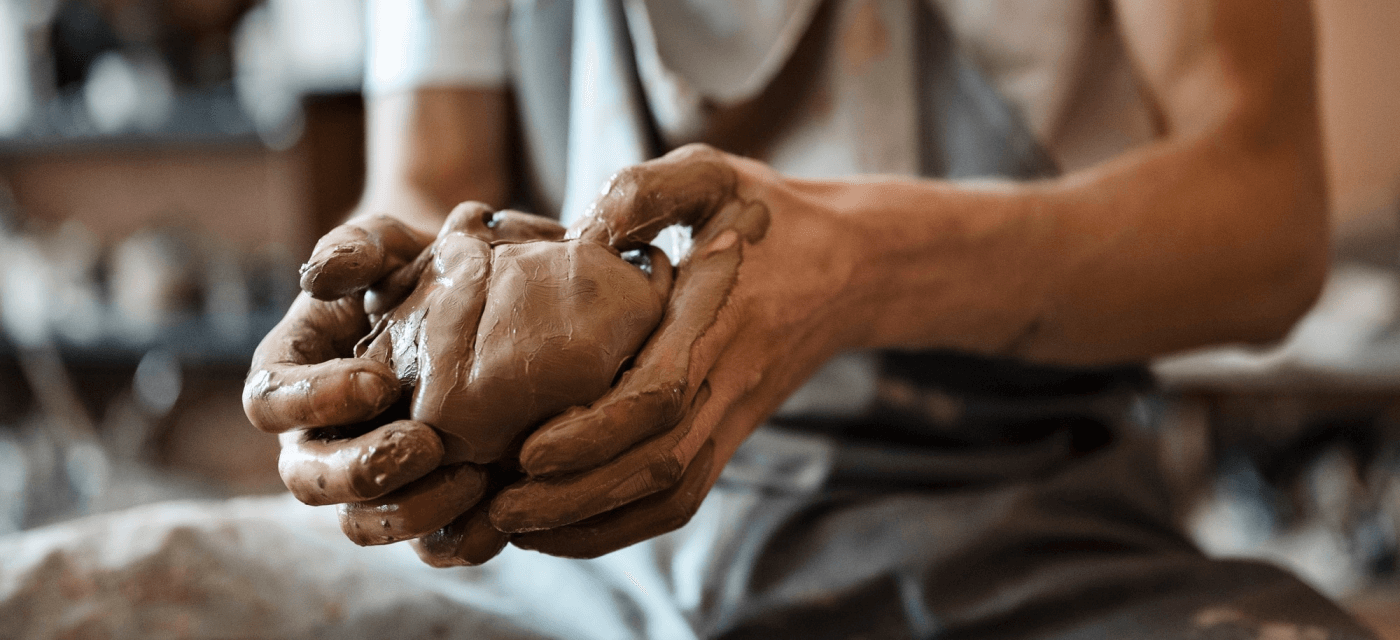
Sculpture production steps:
Natural special mastic preparation and screening, spray water to wake up mud more than 48 hours (winter low temperature for more than 3 days), round sculpture welding sculpture steel modelling skeleton, winding cross-shaped wooden bar on the skeleton to support the mud device, density according to the actual situation in order to ensure that the mud on the big mud after not partially off the mud for the principle of the sculpture on the skeleton of the large gap in the pavement of the metal mesh, which can reduce the amount of mud to reduce the total weight to ensure that the sculpture does not collapse, the idea of safety and at the same time to avoid collapsing the scrapping! Rework. If it is a bas-relief need to carpentry board laying baseboard on the board every 15cm nails, nails into half of the other half exposed to facilitate the hanging mud, the other in the nails on the longitudinal and transversal winding fine wire is also convenient to hang the mud. Other details and processes are omitted.
The second step on the clay to cover the sculpture modelling. When the clay is finished, use a wooden mallet to smash the clay and make up for the empty space between the clay. After all the clay is applied, the big shape is constantly adjusted. Modelling is not allowed to rework the skeleton to rest until satisfied, the above must be completed by professional sculptors. From this stage onwards, the sculpture must be sprayed with water frequently to keep it from cracking, and halfway through the break, it should be covered with plastic film to moisturise it until the sculpture mould is completed. Other details and processes are omitted.
The third part of shaping, professional sculptor to complete, shaping process sculptor at any time in the water spray at any time shaping, specific details of other processes are brief.
The fourth step of the sculpture is completed, notify the party to review the big shape and put forward comments or modifications. Continue to continue to adjust and detail shaping to achieve perfection, all complete modelling after the overall push light clay sculpture, the use of scraper for push light. Other details and processes are omitted.
The fifth step is to enter the turning stage, using slices on the clay sculpture to divide the design of the block mould, and then sprayed with soapy water as an isolation protection. Professional turnover technicians proportion gypsum slurry on the sculpture covered, specific gypsum slurry outer layer of the inner layer of different water ratios by professionals to master and to complete. After the plaster is hardened and dried, start to take off the mould, before taking off the mould, we have to fix the gripper on the block, the gripper is made by gypsum numbing stakes. Other details and processes are omitted.
Sixth step after demoulding to remove the residual mud on the block mould, after finishing the plaster mould for detailed repair, make-up grinding. The mould is then polished with a metal copper mesh. Other details and processes are omitted.
The seventh part of the glass fiber reinforced plastic, mixing good resin to add catalysts and fillers and colour rendering agent, etc., and pay special attention to the safety of chemical solvents to prevent the occurrence of fire. The first layer of resin sizing, the second layer with glass cloth resin with sizing, generally need three to five layers of sizing process. Formation thickness according to the sculpture to choose, super-large sculpture needs 4 layers and above, thickness from 0.5 to 2cm according to the size of the sculpture to choose. Specific other details and processes and processes are not repeated. In this paper, the process is only a general process.
The eighth step of assembling FRP split module for the combination, the specific combination of techniques and processes briefly. After assembling the seam levelling and reinforcement, the internal to establish a permanent steel support system skeleton. Finally sanding, with different sandpaper models for coarse and fine grinding water grinding, most of which must be done manually machine grinding can not be rounded natural and difficult to completely without trace, so it must be hand sanding paper. Other details and processes have been omitted.
The ninth step on the colour, on the base colour, on the colour painting, on the outer protective coating, etc. Specifically abbreviated, such as the need to cast bronze cast bronze sculpture only on the base colour and the outer layer of smooth paint layer. Other details and processes are omitted.
Summary: the above steps to complete the sculpture of the basic process flow, omitted a lot of processes and details of the sculpture of the production process can not be fully introduced here. Finished product. In this there are many details of the process need to be completed by professionals here will not be introduced in detail, in short, the process of many, the process points are also a lot of carelessness will cause rework and scrap, no professional experience is difficult to complete.